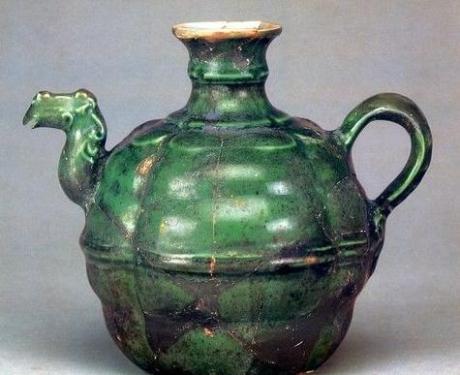
In the history of Chinese ceramics, the use of patina was quite early. In the Han Dynasty, there was precedent for the use of copper as a coloring agent to burn lead green glaze. The Tang Dynasty was widely used in the production of Tang Sancai. During the Song and Jin dynasties, the appearance of green enamel products in Cizhou kiln indicates that the craftsmen have been able to use them harmoniously and skillfully.
Ming Yongle's ChaoYuan plant porcelain technology has been significantly improved, and the low-temperature green glaze gradually develops toward diversification. According to whether the surface of the porcelain glass is glazed when firing, the green glaze utensils can be simply divided into two categories: the green glaze of the female embryo and the green glaze on the glaze.
The prime green enamel green fetal green glaze is applied directly to the surface of a primed green tire and then directly applied to the green glazing at a low temperature. According to the production characteristics, can be divided into monochrome glaze products and three-color products.
Usually, the royal factory independently applies a low-temperature green glaze to a single-colored glaze on the surface of a well-finished prime tire. In order to add artistic effects, the factory will also describe and stack various patterns on the surface of the prime tire. The monochromatic green glazes that were fired at the beginning of the Ming Dynasty are rare, and the handed down items only show the Xuande green glaze bowls that were housed in the Taipei Imperial Palace (Weibo).
Su San Cai is the most common green feast in the Ming Dynasty and other colored low-temperature glaze combined (such as sauce, purple, yellow, etc.) fired utensils. This type of product has been produced in large quantities since the Yongle period. Xuande, Chenghua, and Zhengde are all commonplace. It was the largest cryogenic green enamel utensil manufactured by the Royal Factory at that time.
The archaeological site of the Jingdezhen Yuchang excavated a relatively special green enamel device. Judging from the hair color, it is more appropriate to classify it as a peacock blue glaze. The peacock blue glaze, also known as "French Blue," is a low-temperature glaze that uses copper as a coloring agent because it is named after a bright blue hue after firing. Due to the partial greenishness of some artifacts, it was also named "Malaka Green" or "Fa Tsui." In addition to different hair color, from the raw materials, firing temperature and production characteristics, low-temperature green glaze and peacock blue glaze is very similar.
During the Yongle Period, the Royal Factory also applied green glaze to the glazed surface of high-temperature fired porcelain, and the second time it was fired into the kiln at low temperature. At this time, the green glaze was used as glaze. Judging from the excavation of the former site of the Imperial Factory, there were not many types of products at the time, which were mainly utensils and slag buckets. In the period of Xuancheng, the variety and quantity gradually increased.
During the Xuande period, the Royal Factory used colorful enamel manufacturing techniques to innovate blue and white color, among which the green color on the glaze was extremely important. During the Chenghua period, the rulers were keen on blue-and-white multicolored, and the bucket-colored porcelain imitating the cloisonne was the pinnacle of the production of colored porcelain in the Ming Dynasty. The role of glaze on the glaze was irreplaceable from beginning to end. In addition, among the colorful porcelains that emerged in the middle and late Ming Dynasty, glazes are still essential.
In the Qing Dynasty, as a whole, the green glaze basically inherited the Ming Dynasty's production methods, but some details have changed slightly in different periods. For example, during the period of the reign of Emperor Kangxi, Su Sancai not only used a large number of dark engraving techniques, but also used ** drawing patterns. In addition, the use of milky white glazes made the products look very different from the past. After the Yongzheng era, not only is the workman's craftsmanship perfect, but the hair color is also more beautiful than before.
Yuzheng Royal Factory also produced a green enamel painting with a painting style similar to Xuande Peacock Blue. The craftsmanship of this kind of utensils is to use **painting on primed fetuses, then cover the green glaze and put it into the kiln at low temperature. Yongzheng Yuchang’s ceramic painting style is rigorous. It combines ** and green glaze perfectly, giving people a fresh, crisp and unique feeling, becoming another bright spot in the Qing Dynasty colored porcelain. This method of production has appeared locally in the three different color and artifacts of the Hessian, but it was not developed as a separate glaze.
In the early Qing Dynasty, many Westerners came to China with the advanced science and technology of Europe, and brought the modern glazing methods to the Imperial Factory in Jingdezhen. Therefore, the Qing dynasty official kiln successively appeared non-traditional glaze products such as barium sulfate and calcium carbonate. Boric acid and other preparations of the glaze, after firing artifacts glaze slightly yellow, slightly green, and turquoise color similar to the "turquoise green." These technological exchanges have led to further complications in the development of green glazes in Guanyao porcelains.
Low-temperature copper green glaze is one of the main color glazes in the production of colored porcelain in the Ming and Qing Dynasties. It is not only suitable for the fetal glaze, but also suitable for the glaze color, so it is widely used in prime three-color, multicolored, and colorful. Even in the later pastel porcelain production, it is an indispensable glaze as glaze on the glaze, which makes people feel that it is everywhere. However, the low-temperature copper green glaze also has its own shortcomings, that is, when making a fetal artifact, because the coefficient of expansion between the tread and the tread is difficult to match, it is easy to form a small open sheet and affect the adhesion of the contact surface. It is easy to peel off after being corroded. Especially in the early Ming period, this phenomenon was particularly prominent. Even so, the low-temperature green glaze is still an economical and simple traditional glaze.
We are the professinaol manufacture in Lining fabric and pocket fabric, for branded garments, made from 100% cotton, Polyester Cotton Fabric , and 100% polyester fabric.
Due Care is taken to avoid slippage problem ensure high durability, color fastness, pilling resistant and soft feel after repeated washes.
Our Lining fabrics, comes in wide range of colors and in plain, herringbone and different dobby weaves, textures and colors.
T/C Pocketing Fabric,T/C Lining Fabric,T/C 65/35 Pocketing Fabric,T/C Pocket Fabric
SHIJIAZHUANG LIANGYOU TRADE CO,. LTD. , http://www.shuolanhome.com